5 Ways to Optimize Your 3D Printing Efficiency and Reduce Costs
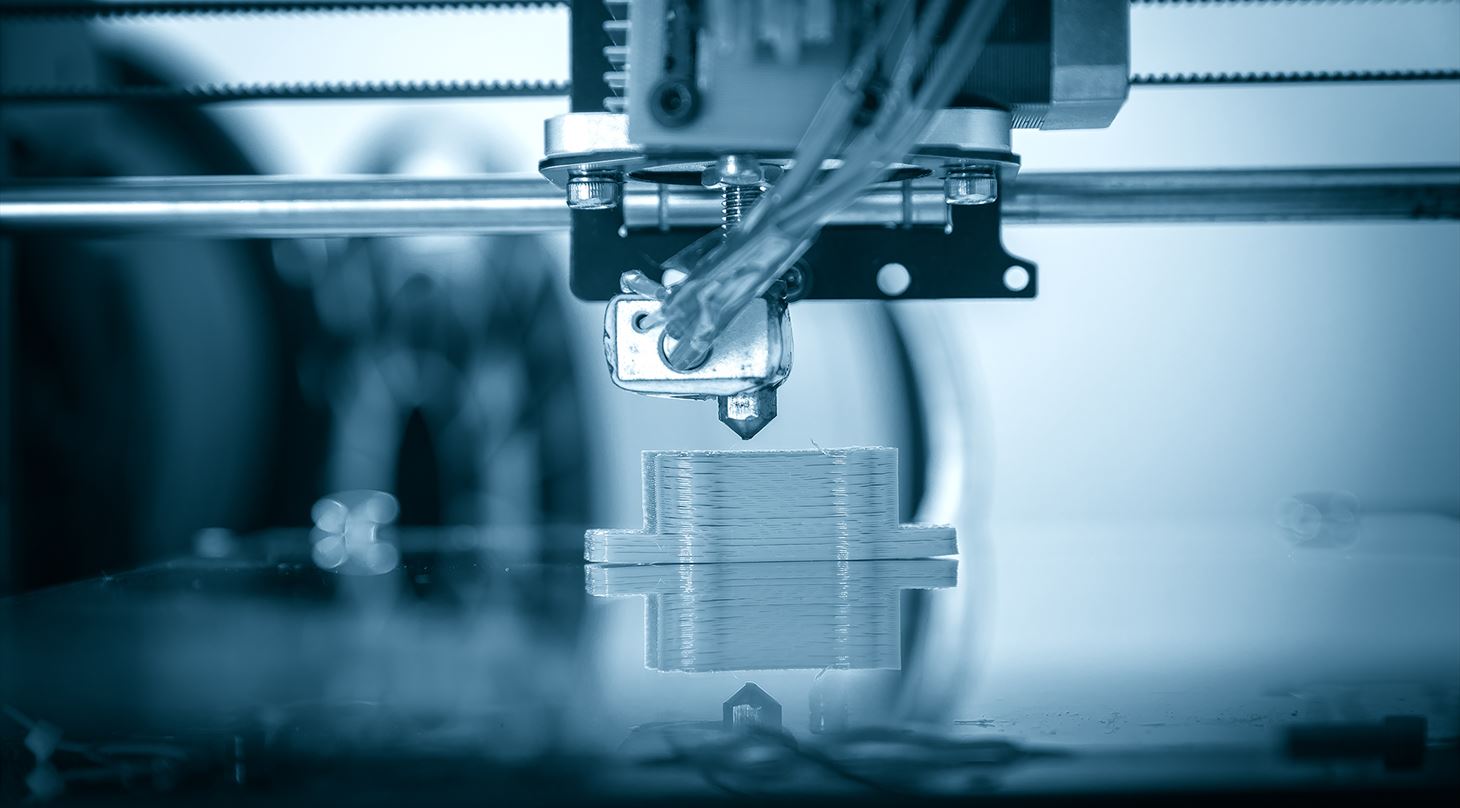
3D printing can be both rewarding and cost-effective when approached strategically. Whether you're a hobbyist looking to maximize your filament usage or a business aiming to improve profit margins, optimizing your 3D printing efficiency is key to reducing costs while maintaining high-quality outputs.
In this guide, we'll explore five proven strategies to help you get the most out of your 3D printer while keeping expenses down.
1. Optimize Your Print Settings
One of the most impactful ways to improve efficiency is by fine-tuning your slicer settings:
Infill Percentage
Most prints don't require 100% infill, which consumes significant material and time:
- Decorative items: 5-10% infill is often sufficient
- Standard household objects: 15-20% provides reasonable strength
- Functional parts with moderate stress: 25-40% offers good durability
- High-stress mechanical parts: 50%+ may be necessary
Layer Height
Layer height directly impacts print time and material usage:
- Detailed models: 0.1-0.16mm for fine details
- Standard prints: 0.2mm offers a good balance of quality and speed
- Quick drafts or large models: 0.24-0.32mm for faster printing
Increasing layer height from 0.1mm to 0.2mm can reduce print time by up to 50% while using the same amount of material.
Print Speed
Faster isn't always better—finding the optimal speed for your specific printer can significantly improve efficiency:
- Test your printer to find its "sweet spot" where speed and quality are balanced
- Use variable speeds for different parts of your model (slower for outer walls, faster for infill)
- Remember that excessive speed can lead to failed prints and wasted materials
2. Batch Your Prints Strategically
Printing multiple objects at once can drastically reduce both time and energy costs:
- Fully utilize your build plate - When printing several small objects, arrange them to maximize build plate usage
- Group similar-height objects - This minimizes unnecessary travel movements
- Consider print time vs. risk - Balance the efficiency of batching against the risk of a complete batch failure
A full build plate typically uses only marginally more electricity than a single small print, as the heated bed and hotend will consume similar power regardless of what's being printed.
3. Choose the Right Materials for Each Job
Different materials have different price points and printing requirements:
- PLA - Economical, easy to print, and sufficient for most non-mechanical applications
- PETG - More durable than PLA but still relatively economical; great for functional parts
- ABS - Higher temperature resistance but requires an enclosure and produces fumes
- Specialty filaments - Reserve these higher-cost materials only when their specific properties are needed
For internal parts or prototypes that won't be visible, consider using less expensive filament or recycled material when possible.
4. Reduce Support Material Usage
Support structures increase material usage and print time while adding post-processing work:
- Orient models strategically - Position parts to minimize overhangs requiring support
- Design with printing in mind - Use 45° angles for overhangs when possible
- Use support settings wisely - Configure supports to use less material:
- Increase support spacing
- Reduce support density
- Use tree supports for complex geometries
- Split complex models - Breaking a model into parts that can be printed flat then assembled can eliminate support needs
Some slicers allow for custom support placement, letting you add supports only where absolutely necessary.
5. Maintain Your Printer Properly
A well-maintained printer reduces failed prints and extends equipment life:
- Regular calibration - Check and adjust bed leveling, extruder steps, and belt tension
- Lubricate moving parts - Keep rails, rods, and bearings properly lubricated
- Clean your nozzle regularly - Prevent clogs that can ruin prints
- Inspect for wear - Replace nozzles, PTFE tubes, and other consumables before they cause problems
- Store filament properly - Keep filament in airtight containers with desiccant to prevent moisture absorption that leads to failed prints
Even a 5% reduction in failed prints can yield substantial material and time savings over the course of a year.
Measure and Track Your Improvements
To truly optimize your 3D printing operation, track your metrics before and after implementing these changes:
- Material used per print
- Print time per model
- Electricity consumption
- Failure rate
- Post-processing time
Our 3D Print Cost Calculator can help you track these metrics and calculate the exact cost of your prints before and after optimization.
Calculate Your Savings
Use our free 3D Print Cost Calculator to see how much you can save by implementing these efficiency improvements.
Remember that the most efficient 3D printing operations balance material usage, print time, electricity consumption, and print quality. By implementing these strategies, you can significantly reduce your costs while maintaining—or even improving—the quality of your 3D printed projects.